OIL&GAS
Rubber expansion joints play a crucial role in the oil and gas industry. They are primarily used to connect pipeline systems, providing flexible interfaces to accommodate stresses caused by equipment vibrations, displacements, and thermal expansion and contraction. These joints effectively absorb and buffer dynamic loads, reducing wear on the pipeline system and extending the lifespan of equipment.In terms of application, rubber expansion joints are widely used in oil and gas transportation pipelines, oil wells, storage tanks, and refineries. When installing, it is essential to ensure that the material of the joint is compatible with the conveyed medium to resist chemical corrosion and withstand high-temperature and high-pressure environments. Additionally, proper installation and regular inspection and maintenance are crucial for ensuring the performance of rubber expansion joints.
In the oil and gas industry, Songjiang rubber expansion joints and vibration isolators can provide high-quality solutions, as follows:
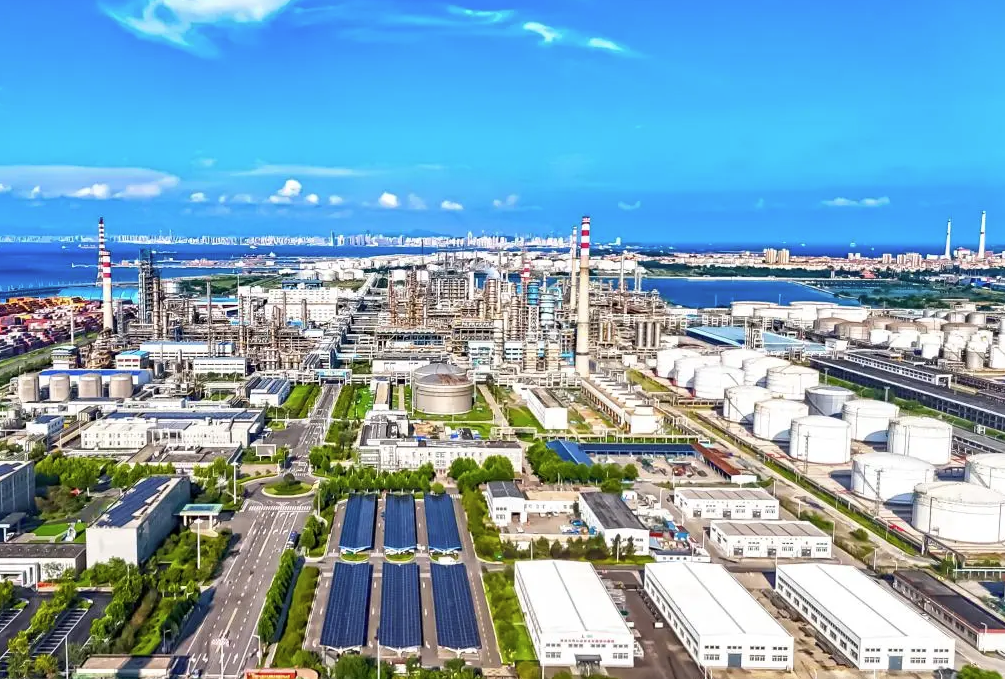
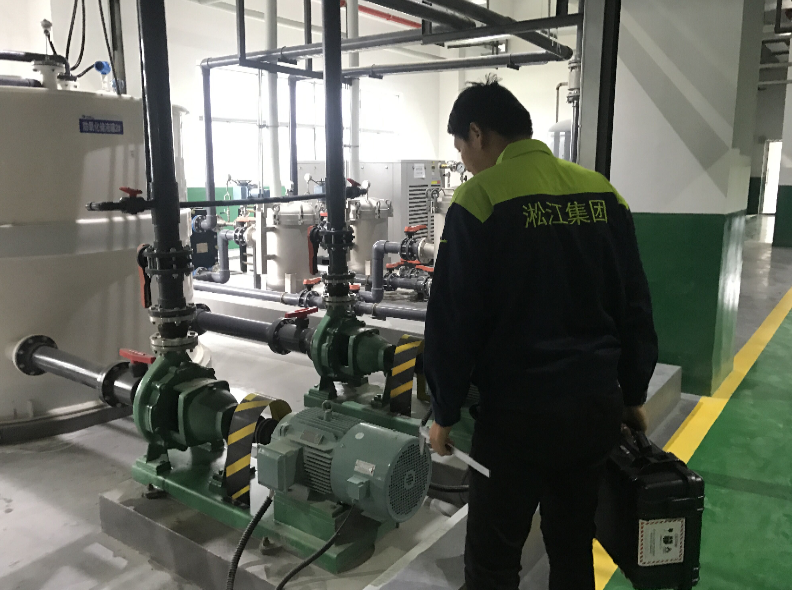
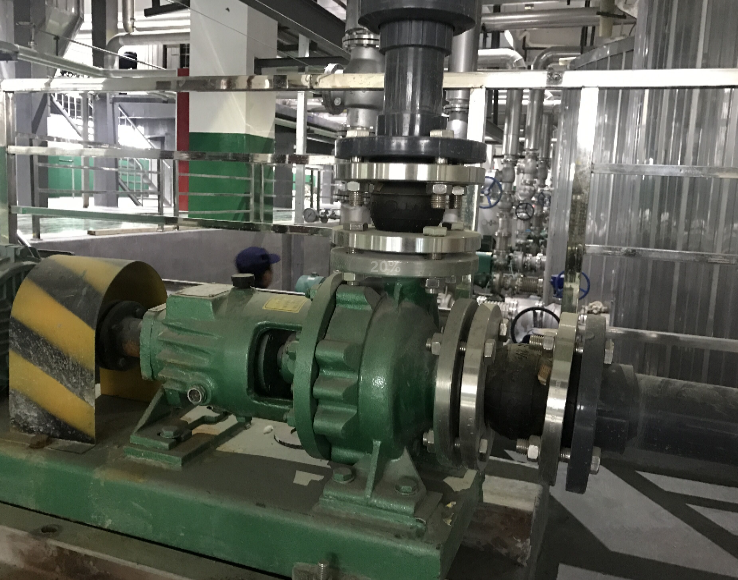
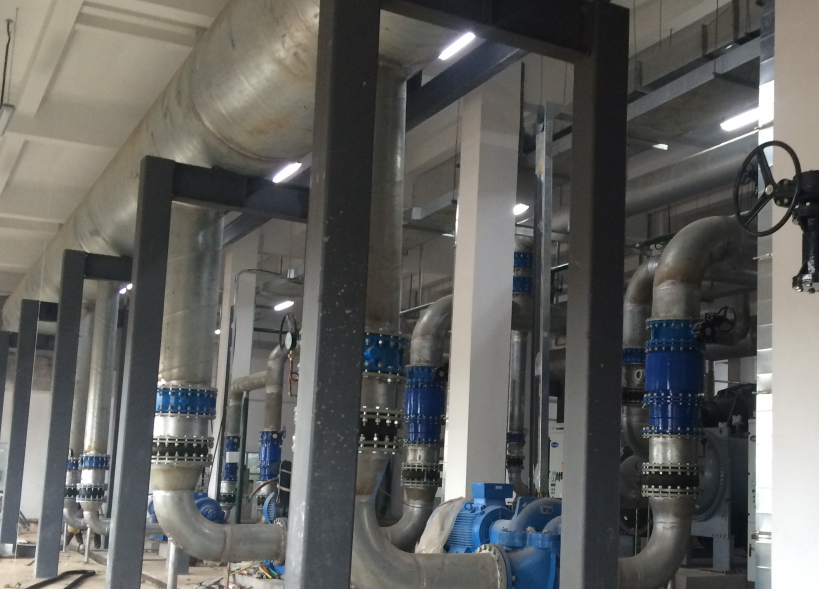
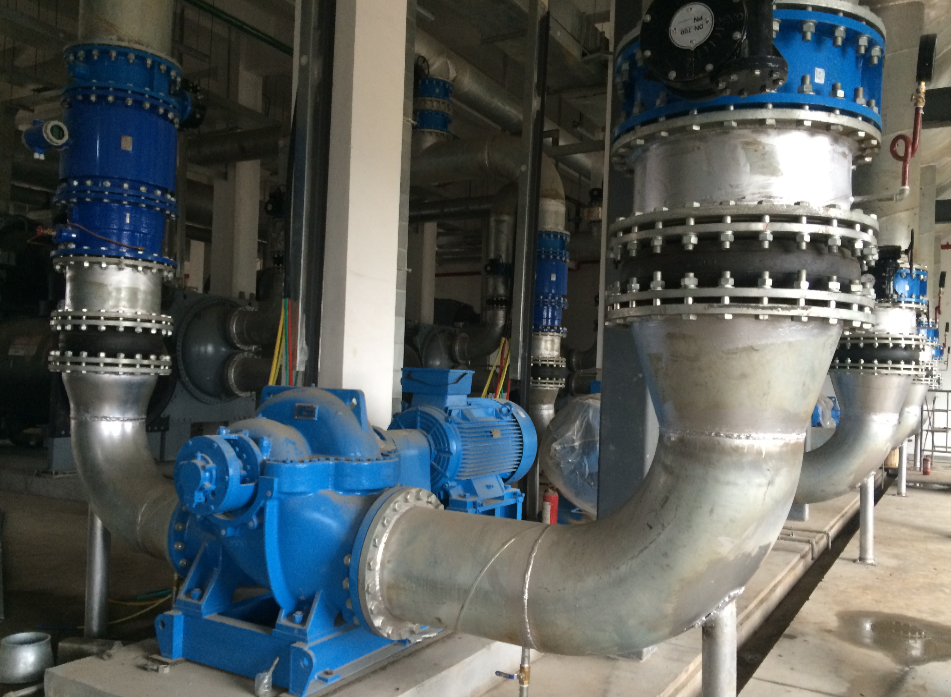
Rubber Expansion Joints Solution
Rubber expansion joints play a crucial role in the oil and gas industry, where equipment and pipelines operate under harsh conditions, including high pressures, temperatures, and exposure to corrosive substances. Here’s an overview of how these solutions support oil and gas operations:
1. Vibration and Noise Reduction
Rubber expansion joints effectively dampen vibrations from pumps, compressors, and other rotating machinery, which helps prevent damage to piping systems. By reducing noise and vibration, these joints also improve the overall work environment, protecting both equipment and personnel.
2. Thermal Expansion and Contraction
In oil and gas applications, pipelines undergo frequent temperature changes that cause expansion and contraction. Rubber expansion joints absorb this movement, preventing pipeline stress and potential cracking, which is essential for maintaining the integrity of the pipeline system.
3. Corrosion Resistance
Rubber expansion joints are designed with elastomers resistant to oils, gases, and chemicals commonly present in the oil and gas industry. Materials like EPDM, Nitrile, and Chloroprene offer strong resistance to chemicals and temperature variations, providing a durable solution for corrosive environments.
4. Pressure and Flexibility Handling
These joints accommodate both high pressure and lateral, axial, and angular movement. This flexibility is critical in complex piping networks, as it prevents rigid connections and reduces the risk of pipeline leaks or ruptures.
5. Shock Absorption
Oil and gas operations often involve high-pressure surges and flow irregularities. Rubber expansion joints absorb shock loads and pressure surges, which helps protect sensitive components in the piping systems and minimizes the risk of system failure.
6. Enhanced Safety and Longevity
By accommodating pipeline movement and isolating vibrations, rubber expansion joints extend the life of the piping system, reduce maintenance costs, and enhance safety. These benefits are essential for critical infrastructure in oil and gas, where downtime or failures can be costly.
Common Applications in Oil and Gas:
- Pumping Stations: To isolate vibrations from pumps and reduce noise.
- Refineries: To handle high temperatures and corrosive materials.
- Offshore Platforms: To manage movement and environmental stresses.
- Pipeline Systems: To accommodate thermal expansion and protect connections.
Why Choose Rubber Expansion Joints for Oil and Gas?
The unique properties of rubber expansion joints—flexibility, durability, and resistance to harsh conditions—make them ideal for oil and gas applications. They help maintain operational efficiency, reduce repair needs, and support safe, reliable, and long-lasting infrastructure.
Vibration Isolators Solution
Vibration isolators are essential in the oil and gas industry to maintain equipment stability, protect pipelines, and ensure smooth operation in challenging environments. Here’s how vibration isolators support this industry:
1. Vibration and Shock Reduction
Heavy machinery like compressors, pumps, and turbines generates significant vibration and shock, which can transfer through piping and equipment. Vibration isolators absorb these forces, reducing wear and tear on components and preventing premature failure.
2. Enhanced Safety and Reliability
In high-risk environments, reducing vibration is critical for safety. Vibration isolators improve the stability of sensitive equipment, reducing the chance of leaks or ruptures in pipelines and ensuring a safer operating environment.
3. Noise Control
Vibration isolators also minimize noise from equipment, which is beneficial in maintaining a quieter work environment and can help meet regulatory noise requirements, especially in offshore and enclosed facilities.
4. Protection Against Environmental and Operational Stress
Vibration isolators are designed to withstand extreme temperatures, pressures, and corrosive environments typical in oil and gas operations. They protect equipment from these stresses, helping extend the life of critical infrastructure.
Common Applications in Oil and Gas:
- Pump Stations: To isolate vibrations from pumps and improve operational stability.
- Pipelines: To prevent vibration transfer and potential structural damage.
- Compressors and Turbines: To ensure smooth operation by minimizing mechanical vibration.
Benefits of Using Vibration Isolators
Vibration isolators contribute to longer equipment lifespans, reduced maintenance costs, and improved safety. They are an essential solution for ensuring operational efficiency and protecting infrastructure in the demanding conditions of the oil and gas industry.
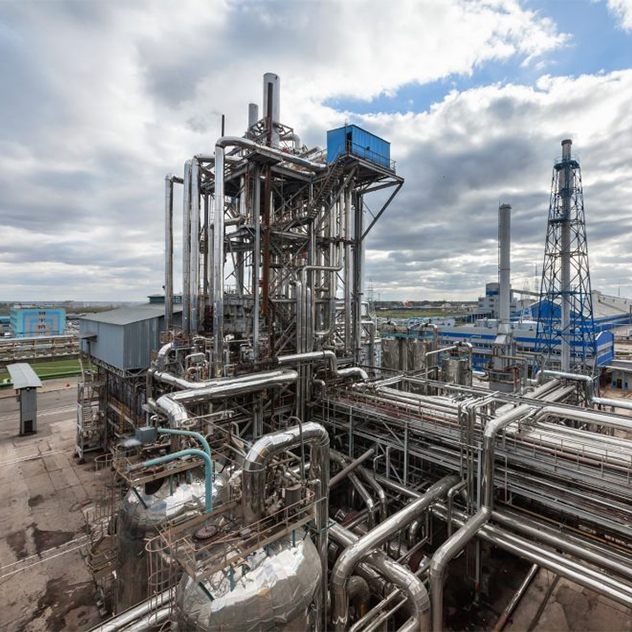
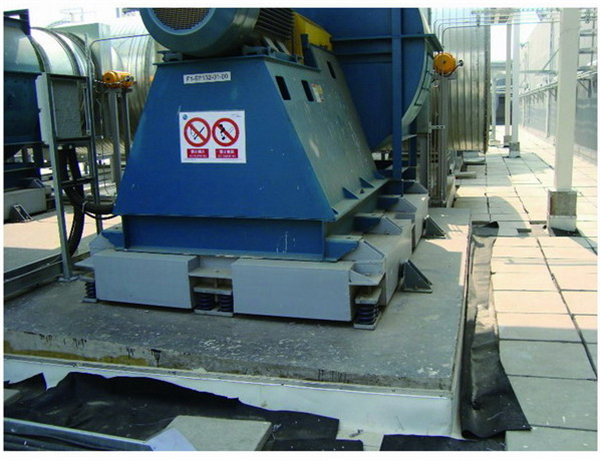
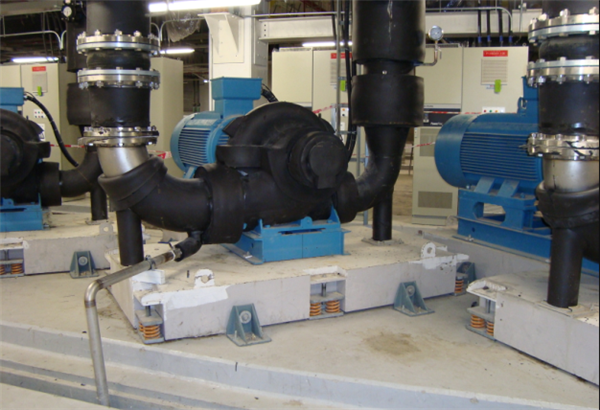
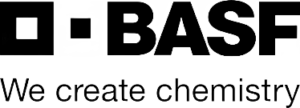
BASF China is upgrading its production system with metal hoses, rubber expasion joints, and rubber /spring vibration isolators for a comprehensive overhaul.
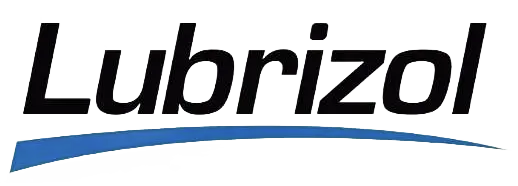
Spring isolators for the Lubrizol specialty chemicals project in Shanghai, aimed at upgrading and retrofitting vibration control in the factory's chemical piping system.
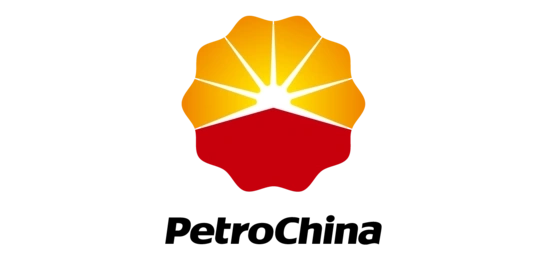
Provide wear-resistant and oil-resistant rubber joints for the mud piping system of China Petroleum Corporation (CNPC) Chuanqing Drilling Engineering Company.
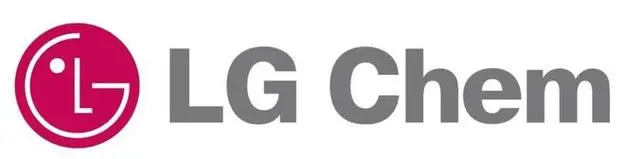
LG Chem's Guangzhou factory is undergoing a complete overhaul of its ducting system, utilizing corrosion-resistant isolators, which provide excellent vibration reduction.
Other Projects Involved by Songjiang - Reference List
The China National Petroleum Corporation (CNPC) Chuanqing Drilling Engineering Company mud pipeline project uses oil-resistant and wear-resistant rubber joints, available in two types: one lined with PTFE and the other an oil-resistant rubber expansion joint with a wear-resistant flow tube.
The Lihua Oil and Gas Recovery Project utilizes rubber expansion joints. Our factory also produces stainless steel metal hoses and PTFE rubber joints.
We supplied rubber expansion joints for the Shell Zhuhai Lubricants Project, which uses joints made from natural rubber and carbon steel flanges.
Our high-quality PTFE rubber expansion joints are used by many oil drilling teams, including the first fully hydraulic intelligent drilling rig in Asia.
The Sinopec Qingdao Refinery and Petrochemical Project employs rubber expansion joints made from natural rubber and connected with American standard carbon steel flanges, featuring limit devices.
We provide rubber joints for electric power companies for shock absorption and noise reduction. For example, the Zhejiang Changxing Hanergy Thin Film Solar Project uses stainless steel 304 flange rubber expansion joints.
The Qinghai Delingha Shanggu Energy Project uses our large-diameter rubber joints, typically equipped with anti-pull rods.
The Qingdao Energy Thermal Power Project incorporates damping spring shock absorbers, for which we supply various rubber joints and dampers.
The Sichuan Pengshan Yabao annual production of 50,000 tons of lithium hydroxide battery materials project utilizes large-diameter EPDM rubber joints made from 100% pure natural rubber without recycled materials.
The Hefei Thermal Energy Center Project uses our stainless steel metal hoses. We also manufacture spring shock absorbers and other products.
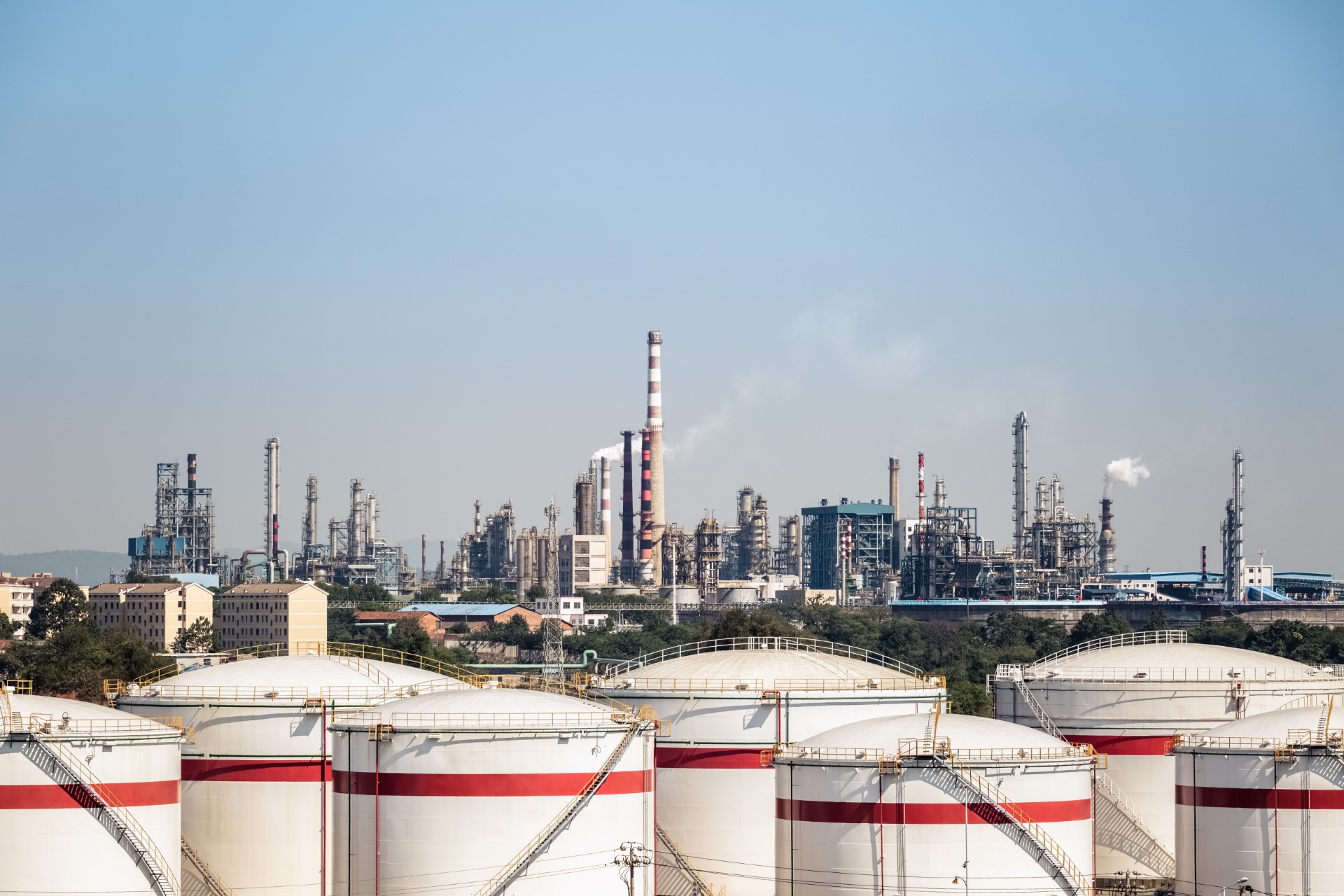